Laser Cleaning
Process highlights
Laser cleaning is perhaps one of the most famous class IV laser applications as it has a very wide variety of use cases. Lasers have revolutionized the cleaning market as it brought new perspectives if compared to other traditional processes such as chemical cleaning, sand blasting or dry ice (cryogenic) cleaning. In fact, laser cleaning is a very versatile solution as it can be very efficient for removing tenacious dirt layers as well as, in the opposite side of the spectrum, eliminating thin coating in a much more selective and precise way than other processes.
In addition to its unmistakable efficiency, laser cleaning offers an environmentally friendly alternative as it is consumable-free and does not use any harmful substances. In addition to this, it is a less noisy process than sand blasting or dry ice cleaning.
Why choosing ShockLite’s laser sources over other lasers?
A vast majority of laser cleaning setups integrates continuous (CW) or pulsed fiber lasers. Before introducing the main difference between our offer and existing laser cleaning sources, let’s make a quick recap on two paramount notions: peak power and average power.
The peak power is the maximum optical power that a pulse will reach. It characterizes the mechanical shock intensity that will be generated by the laser pulse. On the other side, the average power is the mean power emission over time and rather corresponds to the amount of heat that is brought by the laser beam.
In contrast with our fibered laser source, fiber lasers generate low peak powers, hence lower mechanical shocks, while they bring more heat. This large amount of heat can be very detrimental in some applications as it can irreversibly leave traces on parts. Precision manufacturing molds are an example where such marking is prejudicial as it would leave a trace on all the following manufactured parts.
Laser Cleaning solutions we offer
The LightPanther system permits to have large peak powers at the fiber output. These peak power levels make it possible to remove various types of layers ranging from thin paints to thick rust. The system can be integrated in cleaning machines.
We can additionally support customers to find the perfect process parameters (energy, overlap etc) by performing tests on relevant parts with our internal laser cleaning platform.
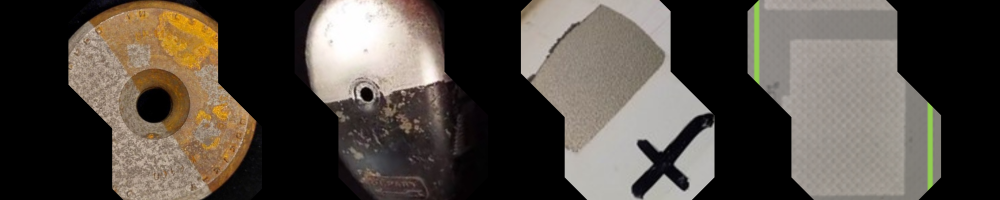